How can I support you?
Unexplained claims
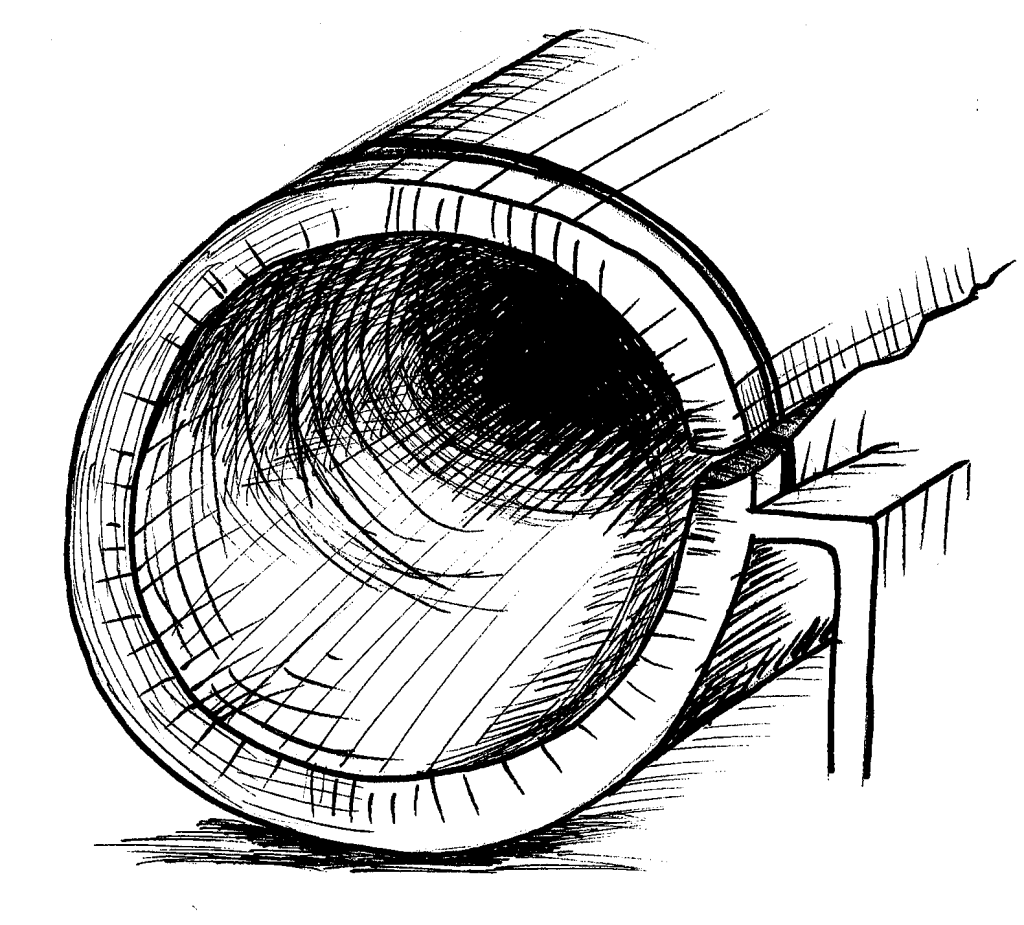
Damage to the product occurs from time to time, whether during in-house tests or, in the worst case, at customer's site. Part of good product development is finding the cause of damage and thus avoiding it in future.
- Verification of hypotheses on the cause of damage through simulation
- Reduction in the number of tests
- Verification of the applied loads and boundary conditions
- Checking of the action to prevent the cause
These are typical simulations using the fine element analysis.
Damage to production lines can also occur. A detailed investigation into the cause prevents future production shutdowns.
Warranty and goodwill costs are too high
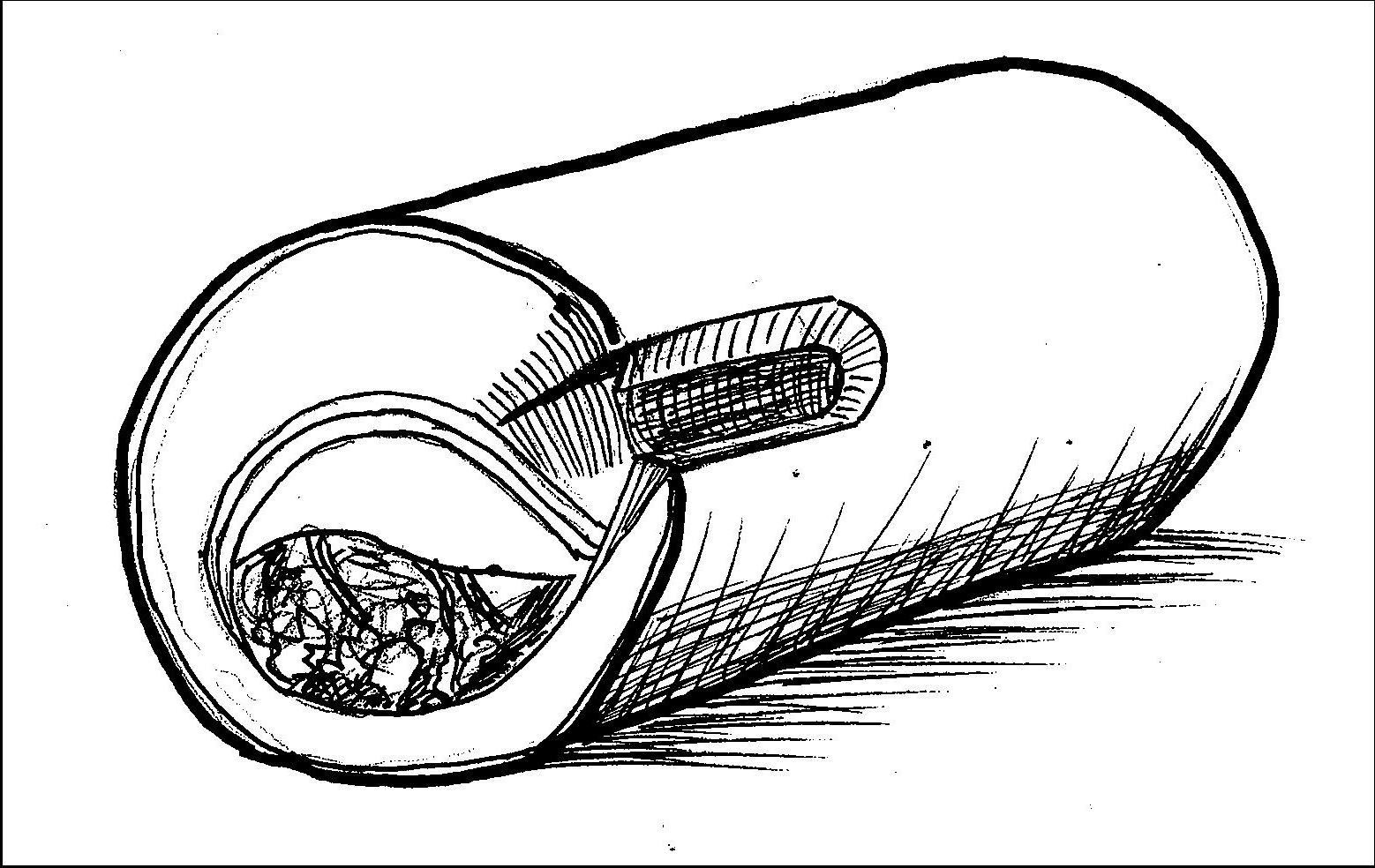
High warranty and goodwill costs indicate systematic problems. Analysing the causes is of existential importance here. Simulations can be used to check various damage hypotheses and test possible countermeasures.
- Cracks or fractures: Calculation of static strength or fatigue life
- Wear: Checking the deformations and pressures
- Temperature increases in bearings: Recalculate local pressures and forces
- Dynamic conditions: Determine velocities and accelerations and the resulting forces and torques
Movements do not run smoothly or vibrate
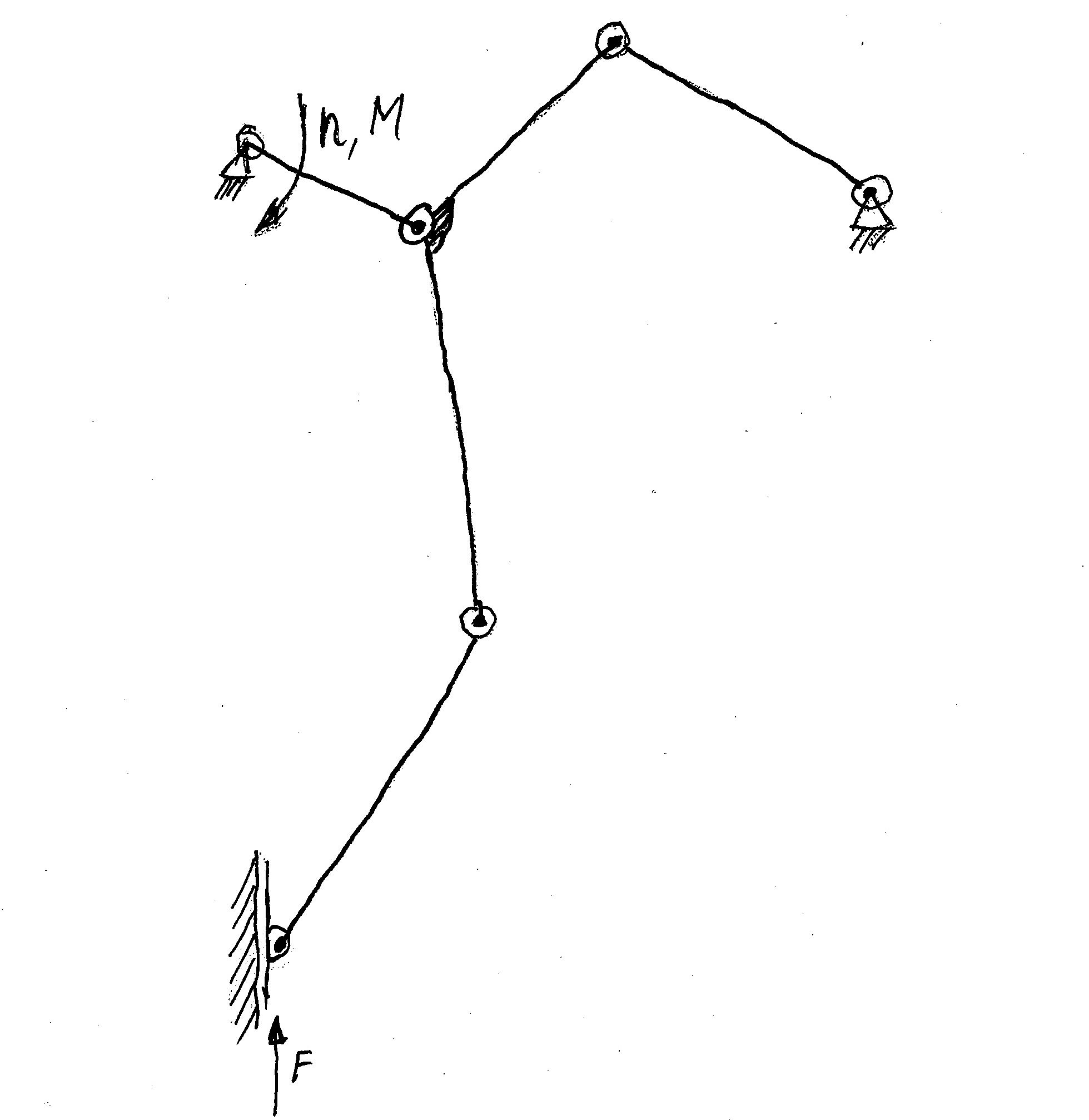
Moving systems, such as kinematics for transporting or positioning parts, can vibrate and therefore be inaccurate. Or the drives can have high current peaks.
Dynamic processes are simulated, checked and optimised using multi-body simulation.
- Higher cycle rates
- Better positioning accuracy
- Less vibrations
- Reduction of current and torque peaks
- Smaller drive units
- Reduction of mass inertia
Material costs are too high
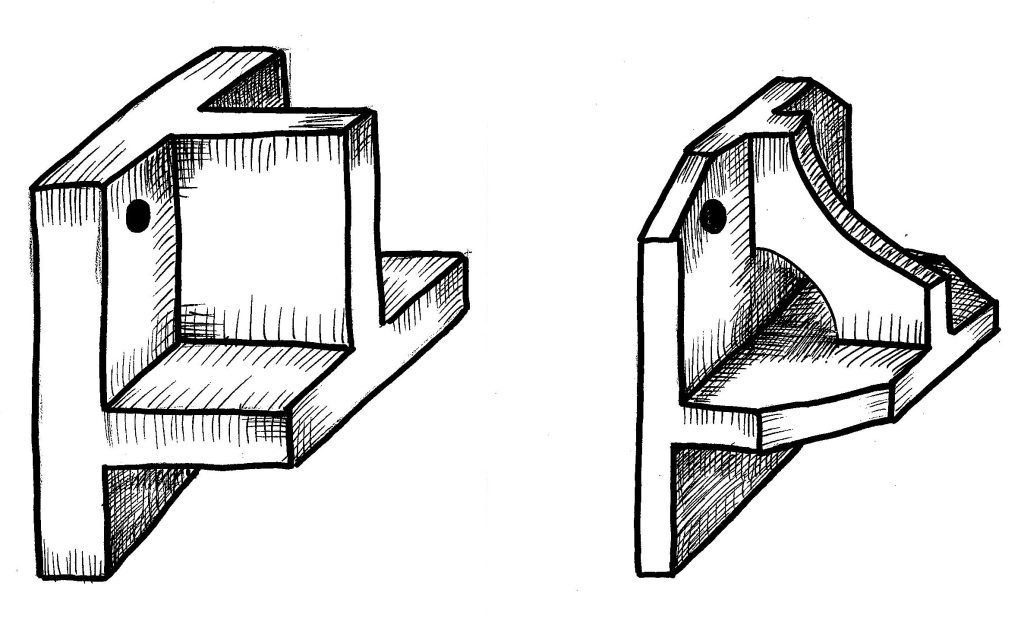
The material costs are influenced by the quantity used, that is the mass and the material, that is its cost.
- Optimisation of component volume for required stiffness and lifetime
- Reduction of lifetime to what is required
- Use of a cheaper material
These are typical simulations using the fine element analysis.
Production costs are too high
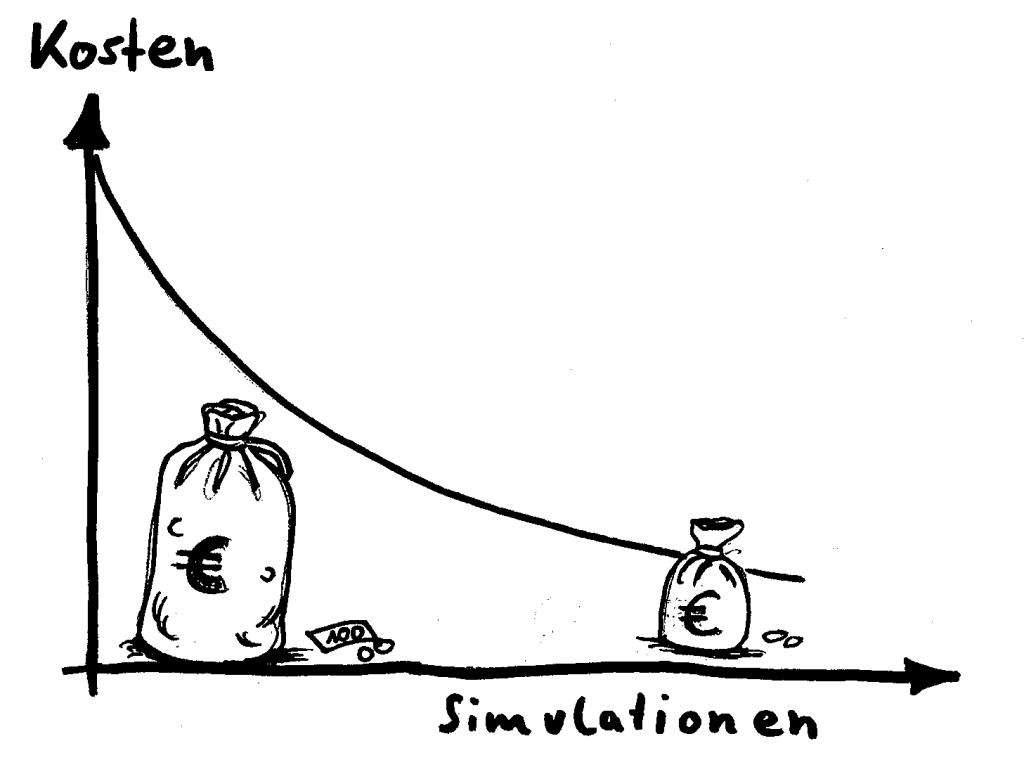
In various ways simulations can help to reduce production costs.
- Reduction of the number of components: Welded connection possible?
Fewer screws needed? - Optimisation of connection elements
- Reduce material costs
- Simpler design, for simpler production
- Reduction of the total mass or design space to make transportation cheaper
Design takes too long
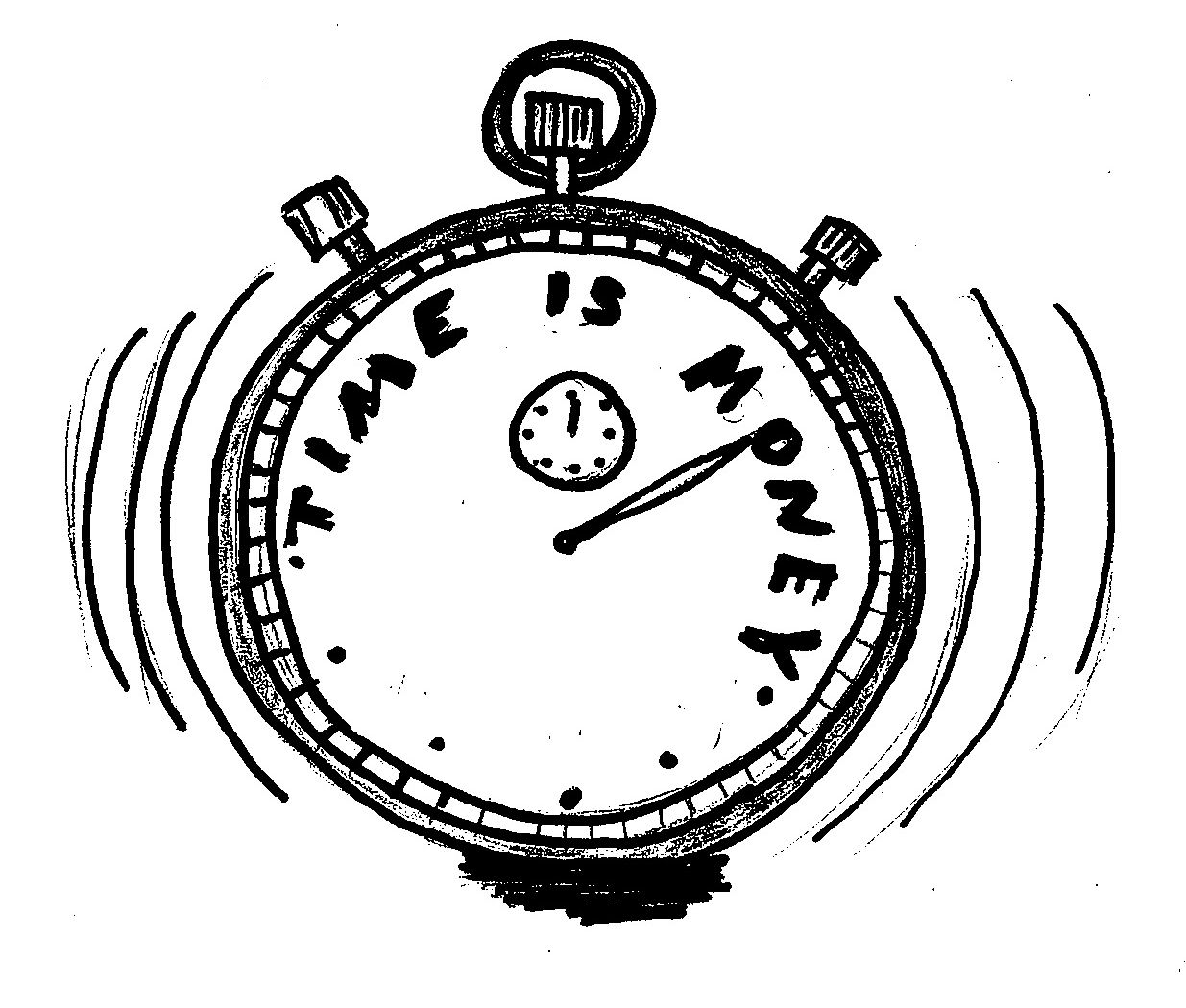
In the case of products that frequently have to be customised, the design must also be redesigned. To do this, all calculations must be carried out again and the components adapted step by step. It is possible to automate this dimensioning process. This speeds up the process and reduces the risk of errors.
Processing times are too long
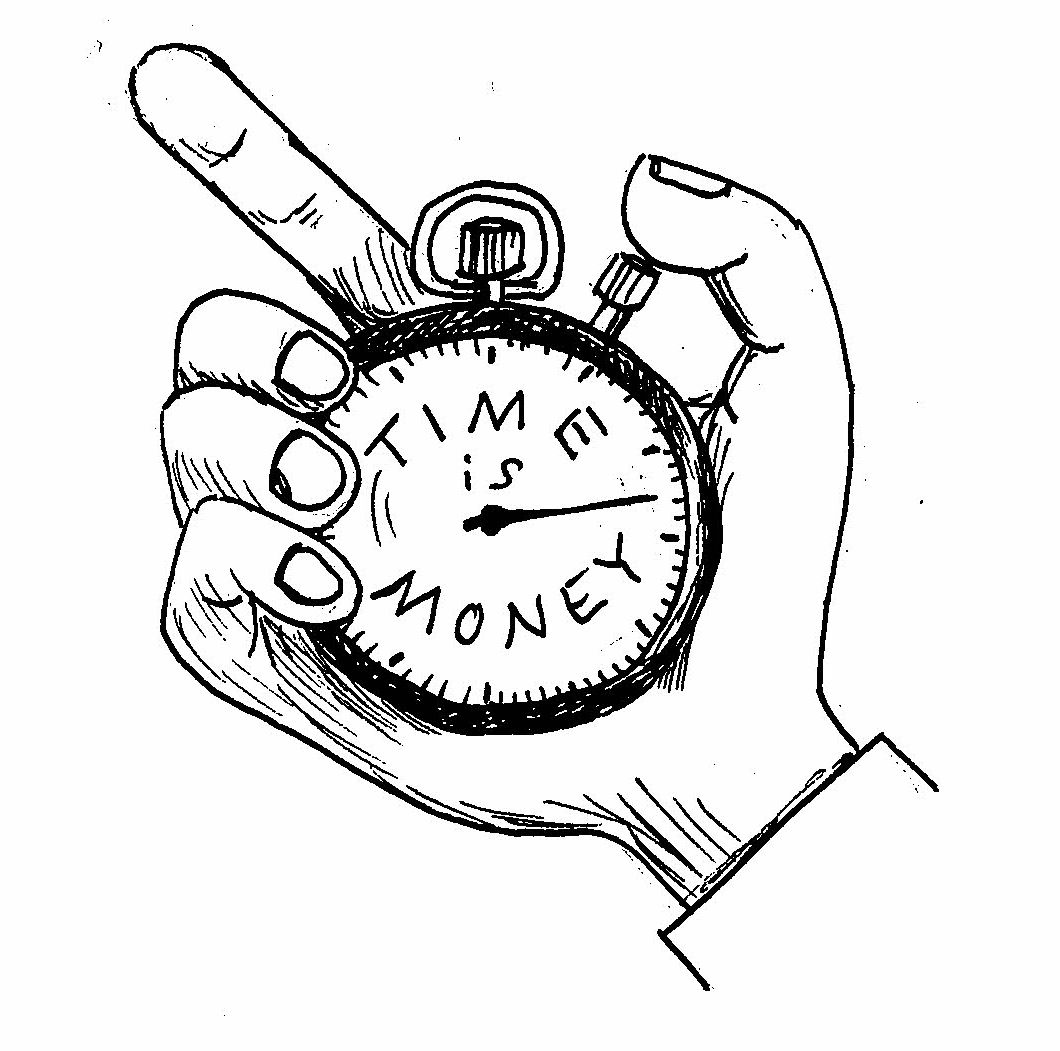
Simulations can be used to check design simplifications that lead to a reduction in production times.
- Reduction of the weld cross-sections to what is required
- Optimisation of connection elements, e.g. fewer bolts, interference fit, etc.
- Reduction of the number of components